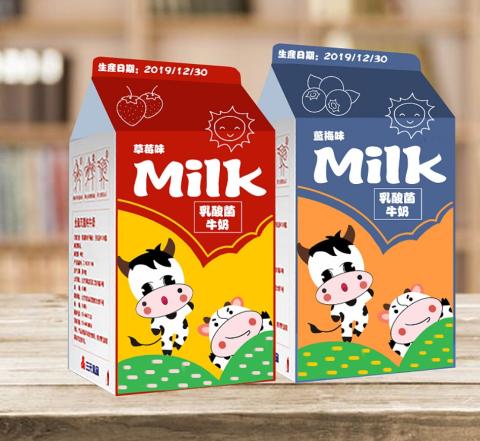
Specification
- Flexography
- White: 205gsm, 215gsm, 225gsm, 240gsm, 290gsm
- Kraft: 195gsm, 200gsm, 219gsm, 230gsm, 270gsm, 300gsm, 328gsm
- Gravure
- White: 205gsm, 210gsm, 215gsm
- Kraft: 300gsm, 305gsm, 310gsm, 320gsm
Liquid packaging board (LPB base paper) refers to primary paper products that are not laminated or coated for subsequent processing into liquid packaging materials. This base paper is specially designed and process-controlled in the production process to meet the performance indicators required for making liquid aseptic packaging containers, such as strength, smoothness, air permeability, health, and safety.
Features
- High Strength: It has high breaking strength and breakage resistance index to ensure that it can withstand the gravity of internal liquid and external pressure without breaking during the process of packaging filling, transport and storage.
- Waterproof and anti-penetration: Although it is paper-based material, by choosing specific fibre raw materials and manufacturing process, it has certain waterproof and barrier properties to prevent moisture and oxygen from penetrating through and affecting the quality of the package contents.
- Food Safety: It meets the safety standards for food contact materials and does not contain harmful chemical substances, which ensures that it will not pose a threat to food safety when it comes into direct contact with food.
- Good printing adaptability: smooth surface, suitable for high-quality printing, can be printed with product information, brand logos and promotional graphics.
Applications
- Liquid packaging paper base paper is mainly used for further processing into various types of liquid packaging containers, such as ambient aseptic pillow packs, brick-type packs (e.g., Tetra Pak, Comet packs), and so on.
- In the food and beverage industry, it is especially used in the packaging of liquid dairy products, fruit juices, tea drinks, alcohol, and other non-carbonated beverage products.
- After laminating or laminating the film to form a multi-layer structure, it enhances its barrier property and shelf-life preservation effect and achieves the goal of maintaining stable product quality and prolonging shelf-life at room temperature.